Case Study of a Stamford Home
By Albert Jensen-Moulton, BPC Green Builders
with Larry Marner, Marner Architecture
BPC has built several houses for clients who also happened to be architects. One of these clients, Larry Marner, recently had an opportunity to design a new home for his family. Above all, he wanted the house to reflect his passion for sustainability and wellness. His goal was to take advantage of the rich breeding ground of ideas in those areas, in order to create a healthy building that has a minimal impact on the environment. He set about designing the house to adhere to the following set of guidelines:
Net zero energy consumption
Net zero energy homes produce as much energy as they consume over the course of a year. There are several ways that energy can be generated onsite to power the home, but the most common is through the use of solar photovoltaic panels.
No fossil fuels
The production and use of fossil fuels like oil and natural gas is the largest contributor to the rising levels of carbon dioxide in the atmosphere. In order to keep his family’s carbon emissions as low as possible, Larry strove to find alternatives to combustion appliances normally used for space heating, hot water, and cooking.
Minimal environmental impact
Theoretically, any size house can achieve net zero energy status. But the additional environmental impacts of materials, land use, and water use must also be considered. Larry committed to building a house with just enough square footage to satisfy his family’s needs and still live comfortably – while preserving as much of the natural surroundings of the site as possible.
Wellness
It was very important to Larry to design and live in an indoor environment that contributes to the well-being of its occupants. In their book Healthy Buildings, Joseph Allen and John Macomber provide empirical evidence that bringing more fresh air into a building and filtering it more effectively is associated with better health outcomes.
In order to achieve the above goals, Larry turned to the principles used to create Passive House buildings. The Passive House standard began in 1991 as a prescription for any building type, old or new, in any climate. Houses built to this standard achieve very low operational energy use by relying on airtight and highly insulated thermal envelopes coupled with mechanical ventilation that provides a constant supply of fresh, filtered air. Other energy-saving measures such as passive heating and cooling, the use of efficient appliances, and innovative hot water systems are often included to help meet the rigorous demands of the program.
During the design process, Larry reached out to BPC Green Builders, and we helped him adjust his design parameters so that the house would closely align with the five basic Passive House principles:
Insulation
Before devising the insulation plan for this house, we first had to clearly define the boundaries of the thermal envelope. In order to reduce the total conditioned area, the partial crawl space under the house was considered to be completely outside of the thermal envelope. As a result, the underside of the house (whether over the crawl space or jutting out over the hillside on steel columns) is insulated with 16” of cellulose (shredded newspaper) packed into the open web trusses that make up the floor deck. Below those trusses, we added a continuous layer of 3” thick mineral wool boards, giving us an effective R-value of 65 for the bottom of the house.
The 2×6 exterior walls are also filled with dense-packed cellulose, but we created an additional cavity on the outside by hanging 12” trusses outboard of the sheathing. This cavity is filled with even more cellulose, resulting in a total exterior wall R-value of 62. A vapor-open weather-resistant barrier protects the cellulose from wind and rain, and allows it to dry to the outside in the unlikely event of moisture infiltration.
At the roof, tapered open-web trusses with an average depth of 28” are again filled with dense-pack cellulose, resulting in an effective R-value of 98. A vapor control membrane (Pro Clima Intello Plus) prevents moisture from accumulating in the roof, and allows any residual moisture to dry to the inside of the house in the winter.
Standard residential building codes call for a level of thermal insulation that often requires foam to be used – especially in homes that are conventionally framed. Spray foam is a petroleum-based product, and the blowing agents used during installation have a very high global warming potential and can be hazardous to the health of the installer. Using carbon-neutral or carbon-sequestering insulation like cellulose can drastically reduce the carbon footprint of a home before it is even occupied.
Air Tightness
Stopping air movement between the exterior and interior of a building helps to reduce heat loss, but it has other advantages as well. A carefully sealed building envelope contributes to long-term durability by preventing damage due to condensation within walls and roofs. It also improves occupant comfort by helping to control humidity levels.
Most common standards required by code for airtightness range between 3 air changes per hour (ACH) and 7 ACH when the building is pressurized to simulate a 15mph wind. It is common to find older buildings that are twice as leaky or worse. At the other extreme, the Passive House threshold for air tightness is less than or equal to 0.6 ACH!
Continuous air sealing is achievable with the proper treatment of transitions between and around windows, doors, roof edges, and foundation walls. With careful planning, air sealing does not introduce a significant added construction cost, and easily pays for itself with the reduction in energy use.
Over the past several years, “smart” air barriers have become more widely available. These membranes, like the one we used here, feature variable vapor permeability in order to control both air and moisture vapor under varying conditions. All joints, penetrations, and seams must be sealed with specially-designed tapes and caulks that work with the membranes to create a complete air sealing system.
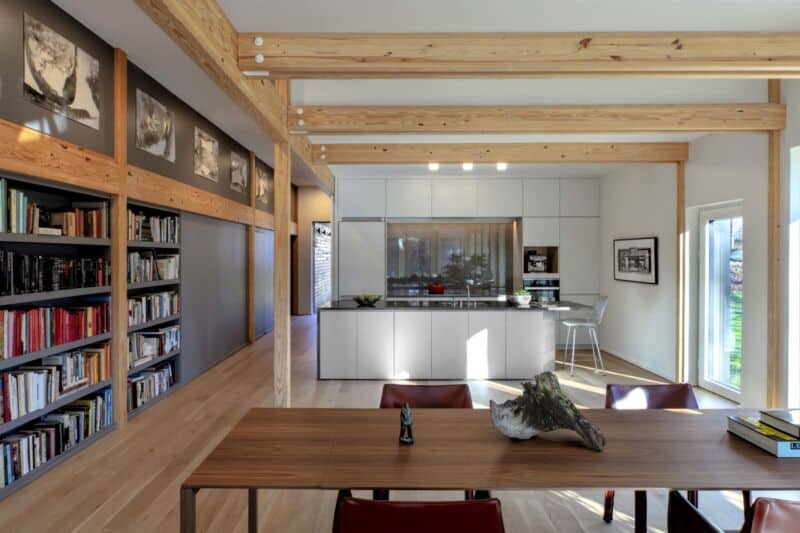
Avoiding thermal bridging
The design of this house necessitated some very strong structural members in several locations: to support the portion of the building that extends out above grade, to brace the glazing-heavy living room in the absence of shear walls, and to create overhangs that provide exterior shading. Steel is the obvious choice for those uses, but steel is a very good conductor of heat, with a R-value of only 0.003 per inch. When steel extends from the outside to the inside of the building envelope, it becomes a thermal bridge between the interior and exterior spaces and reduces the building’s energy efficiency.
Reducing thermal bridging in this case required some careful planning and the use of alternative materials. Structural steel members below the house are separated from the wood framing and subfloor by high-density structural foam wherever possible, and at no point does any steel extend into the conditioned space. Where we needed beams to support shade-supplying overhangs, we turned to laminated timber (glulam). Softwood has an R-value of about 1.4 per inch, so when the glulam beams pass through the building envelope at the 18” thick exterior walls, they have a total R-value of about 25. As a bonus, the glulam beams are a point of visual interest.
Mechanical ventilation
Due to their airtight envelopes, Passive House buildings require mechanical ventilation in order to supply fresh air to their occupants. Air becomes stale when the oxygen is used up by people and other living beings and replaced by CO2 and moisture. Indoor air quality is also reduced by odors from cleaning products, off-gassing from paint and other building materials, and various other pollutants. Bringing in fresh air and exhausting stale air helps to create a healthy home.
The system used to provide balanced ventilation in a Passive House usually includes an energy recovery ventilator (ERV). This machine contains a special core which allows most of the heat and humidity from the stale exhaust air to be transferred to the incoming fresh air during the heating season (and conversely during the cooling season). This air streams do not mix, but the incoming fresh air passes through a MERV 13 filter to remove outdoor air pollutants, pollen, and dust. The ventilation system exhausts air from the bathrooms and kitchen, discharging odors and excess humidity to the outdoors. At the same time, it provides the fresh filtered outdoor air directly to the bedrooms and other living spaces.
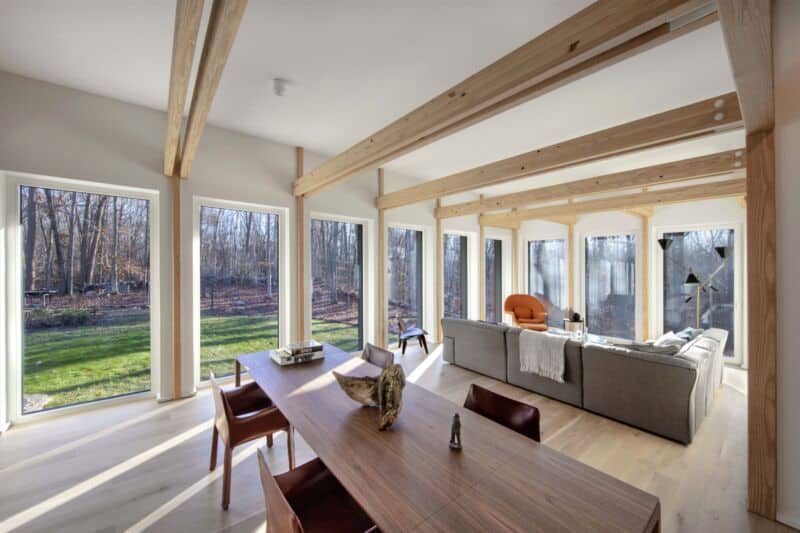
Efficient glazing
Designing windows for this house was a balance between capturing the wonderful views and mediating the local climate. Windows, unlike opaque elements, both lose heat AND gain heat. If made of high-quality components, south-facing Passive House-quality windows can actually GAIN more heat than they lose on an annual basis – effectively turning them into part of the house’s heating system. In our climate, it is best to orient the windows to the south for the maximum gain in heat from the sun during winter. But is also important to provide shading over the same windows in the summer months when the sun is higher in the sky.
We used triple-glazed, airtight windows with insulated frames that provide on average about 4 or 5 times the insulating value of a typical double-glazed window. To give you a sense of how the glass alone functions, a typical double-glazed window in the winter will have an interior surface temperature of about 48 F, contributing to a drafty feeling caused by thermal convection. The interior surface temperature of a properly installed triple-glazed windows is around 60 F, which means that the portions of the room near the windows are as warm as the rest of the room.
Energy Modeling
The five Passive House principles work together as a system, and the behavior of this system under various conditions can be modeled using sophisticated software. BPC Green Builders was able to produce an energy model to see how various parameters interacted with changes in the design. The model takes into account the insulation levels in each part of the house, the overall air tightness, any thermal bridges, the efficiency of the mechanical ventilation, and the various window parameters (size, location, orientation, solar gain, shading, etc.). This was a crucial step in the engineering process, without which we could not have developed the most cost-effective way to meet the Passive House standard.
The energy model also helps to determine the size and design of the heating and cooling system by calculating the peak heating and cooling loads. These take into account the solar gain through the south facing windows, the heat gain from electrical equipment and occupants, the energy loss through the ventilation system, and the thermal transmission loss through the enclosure. The peak heating load of a Passive House is relatively small – often as little as one tenth of the heating load of a conventionally built home. This low load means that much smaller heating and cooling systems can be installed. And because Passive Houses are so highly insulated and airtight, they tend to maintain a comfortable temperature for long periods without using much additional energy.
Getting to Net Zero Energy
In order to achieve net zero energy designation, this house will have to produce as much energy as it uses each year. This includes the energy needed to heat and cool the home, provide hot water, illuminate it, power its appliances, and provide electricity for any other uses (often called “plug loads”). The yearly energy use can be determined at the time of design by computer modeling that takes into account the heating and cooling loads, the efficiency of the HVAC equipment, and the estimated appliance use and plug loads. This proscriptive path can help a builder properly size a solar photovoltaic (PV) array to be installed at the time a house is built. We are choosing to take a performance-based approach and are instead tracking our energy use over the course of our first year living in the house. This can be done by simply tabulating kilowatt-hours on electricity bills, or by installing equipment that offers more detailed monitoring of individual appliances.
If solar PV panels are not installed up front, then certain preparations need to be made for installation at a later date. The layout of the PV array should be determined in advance, as the roof has to be designed to carry the additional weight of the array and oriented in a manner that provides the best possible solar exposure.
Although it is possible to use gas-fired heating, hot water, or cooking appliances and still achieve net zero energy, running the entire house on electricity makes the best use of the on-site renewable energy. It reduces the dependence on fossil fuels or nuclear energy that power the local grid, and avoids the transmission losses that are an inherent part of that system. And by not using combustion appliances, the risk of fire is greatly reduced. But perhaps the greatest benefit from an all-electric home is to the health of its occupants, through the elimination of carbon dioxide and other harmful by-products of combustion.
Getting to Healthy Building
There are several other ways in which the goals and methods used in the design and construction of net zero energy homes result in a healthier building. By making the building airtight and supplying fresh filtered air, we have the ability to control and monitor the five basic indoor air quality factors:
Temperature
The level of insulation and airtightness required by a Passive House results in a temperature differential between the window surface and the adjacent air of no more than 7 degrees, and the difference between the air temperature at your head and feet of no more than 3 degrees.
Humidity
Too much moisture in the air can be uncomfortable, and can cause condensation and an increased risk of toxic mold. Too little moisture leads to cold and flu symptoms. The cooling system extracts moisture from the air in the summer months, and energy recovery ventilator preserves moisture created by cooking and showering during the heating season when a conventionally-built house would typically become very dry due to air leaks.
CO2
Indoor exposure to carbon dioxide can impair productivity and decision-making. The ideal range is below 600 parts per million (ppm). The fresh air brought in by the mechanical ventilation system ensures that the concentration of carbon dioxide will stay well below this level.
Chemicals
Toxic chemicals (VOCs) can be found in everyday materials. They can cause skin and respiratory irritation. The ideal range is below 333 parts per billion (ppb). VOCs are typically found in high concentration in glues, paints, and fabric. The interior paint, floor finish, and exterior pine tar finish were all selected for their especially non-toxic qualities. We purposely avoided carpeting, and use a high efficiency vacuum cleaner which has a HEPA filter that we regularly clean.
PM2.5
Particulate matter with a diameter less than 2.5 microns, or PM2.5, is the name given to fine dust or liquid particles that are suspended in the air we breathe. These particles can come from natural sources such as pollen, or from human activities such as fuel combustion. 2.5 microns is 30 times smaller than a single strand of human hair. Too much fine dust can affect serious health problems like asthma and allergies.
Monitoring our indoor air quality is one way to take control of our health and the air we breathe. Devices that track air quality in real time are inexpensive, and are available from new companies like Aclima, Awair, and Yanzi.
BPC Green Builders and Larry Marner achieved a healthier indoor environment with no impact on budget, project schedule, or product performance. We did this by acting on the recent advances in building science and using a builder and an architect who are practiced at the finer construction details of the Passive House standard. When one considers that 90 percent of our time is spent indoors – and anywhere from 50% to 100% of that is at home – the case for a Net Zero Healthy Home is very compelling.
Project photos and information